新能源汽车自动变速器壳体压铸成型技术,解决壳体强度与轻量化难题。
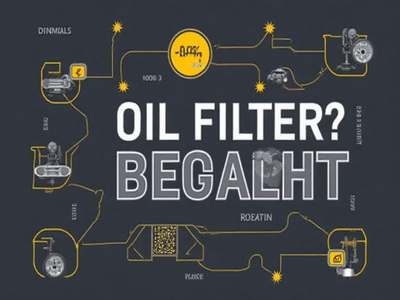
新能源汽车变速器壳体面临的挑战
新能源汽车,作为未来汽车产业的发展重点,其核心部件——自动变速器壳体,正面临前所未有的挑战。壳体既要保证足够的强度以承受复杂的传动应力,又要追求轻量化以提升能效。这就像是在走钢丝,既要稳固,又要轻盈。
解决强度与轻量化难题:压铸技术的新突破
新能源汽车变速器壳体的压铸成型技术,正是为了解决这一难题而诞生。通过特殊的合金配方和压铸工艺,壳体在保证强度的同时,实现了轻量化的目标。这一技术突破,不仅提升了新能源汽车的性能,更为汽车制造行业带来了新的发展方向。
合金配方:精准调控,提升性能
压铸成型技术的核心在于合金配方。通过调整铝合金中的硅、铜、镁等元素的含量,可以实现对壳体性能的精准调控。例如,提高硅含量可以提升壳体的耐磨性,而适量的铜元素则可以增强壳体的强度。
压铸工艺:技术革新,优化成型
压铸工艺的优化同样至关重要。通过优化模具设计和压铸参数,可以实现对壳体成型的精确控制,减少缺陷,提高产品合格率。此外,采用先进的压铸设备,还可以提升生产效率,降低生产成本。
局部强化:提升耐磨性能,延长使用寿命
新能源汽车变速器壳体在使用过程中,内齿轮承受着巨大的压力和磨损。为了提升壳体的耐磨性能,延长使用寿命,通常会在内齿轮表面进行局部强化处理。微弧氧化技术就是一种常见的强化方法,它可以在齿轮表面形成一层致密的氧化铝保护膜,显著提升耐磨性。
案例分析:技术成果的应用与推广
某新能源汽车制造企业,通过引进先进的压铸成型技术和局部强化技术,成功研发了新一代变速器壳体。该产品在保证强度的同时,实现了轻量化,有效提升了车辆的动力性能和能效。该产品的上市,为新能源汽车行业树立了新的技术标杆。
未来展望:技术创新,引领行业发展
随着新能源汽车行业的快速发展,变速器壳体压铸成型技术将迎来更大的发展空间。未来,技术创新将成为推动这一行业发展的关键。相信在不久的将来,更加先进的压铸技术和材料将会涌现,为新能源汽车的普及和发展提供有力支持。
从新能源汽车自动变速器壳体压铸成型技术,解决壳体强度与轻量化难题。延伸出来,我们谈谈新能源汽车变速器壳体轻量化创新技术。
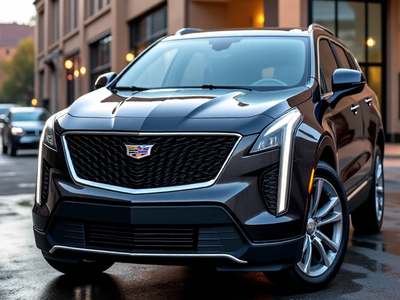
一、新能源汽车变速器壳体轻量化背景
随着全球对环保和能源效率的日益重视,新能源汽车产业迎来了飞速发展。变速器作为新能源汽车的核心部件,其壳体的轻量化设计对于提升整车的性能和续航里程至关重要。本文将探讨新能源汽车变速器壳体轻量化创新技术的应用案例。
二、创新技术:高硅铝合金的应用
为了解决传统铝合金硬度不足的问题,我们采用了高硅铝合金。这种材料在保持良好流动性的同时,显著提高了硬度,从而满足了新能源汽车变速器壳体的耐磨性要求。
在某新能源汽车变速器壳体项目中,我们采用了过共晶高硅铝合金。通过优化合金成分,将硅含量控制在12%以上,不仅提升了合金的耐磨性,还降低了热裂和缩松倾向,提高了压铸件的致密度。这一创新技术的应用,使得变速器壳体的使用寿命得到了显著提升。
三、局部强化技术:微弧氧化方法
为了进一步提高变速器壳体内齿轮的耐磨性,我们采用了微弧氧化方法进行局部强化。这种方法可以在铝合金表面形成一层硬质氧化铝层,有效提升齿轮的硬度和耐磨性。
在某新能源汽车变速器壳体项目中,我们对内齿轮进行了微弧氧化处理。通过在碱性溶液中施加微弧放电,成功在齿轮表面形成了一层厚度约为5微米的氧化铝层。这一层氧化铝不仅提高了齿轮的耐磨性,还增强了其抗腐蚀能力,从而延长了变速器的使用寿命。
四、压铸工艺优化:有限元模拟
为了确保压铸过程顺利进行,我们运用了有限元模拟技术对压铸工艺进行优化。通过模拟分析,我们能够预测压铸件的缺陷,并优化模具设计,从而提高压铸件的合格率。
在某新能源汽车变速器壳体项目中,我们利用有限元软件对压铸过程进行了模拟。通过优化模具的型腔结构、浇排系统以及熔体填充过程,成功减少了铸件中的气孔和冷隔缺陷,提高了压铸件的致密度和表面质量。
新能源汽车变速器壳体轻量化创新技术的应用,不仅提升了变速器的性能和寿命,还为新能源汽车产业的发展提供了有力支持。未来,我们将继续探索更多创新技术,为新能源汽车产业的可持续发展贡献力量。
欢迎分享,转载请注明来源:汽车啦